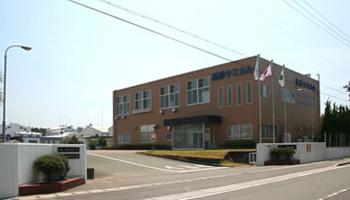
Takasago Chemical Corporation's Kakegawa Factory is the manufacturing base primarily responsible for chemosynthesis for the Takasago Group. Its main manufacturing category is pharmaceutical intermediates and organic electronic materials (OPCs). Based on unique catalyst technology, we contribute to reducing the environmental load from process design stage. We are reducing the emission of industrial waste by reuse of the used organic solvents and promoting green chemistry by linking research and production.
Continuous Production by Flow Reactor
As the first step to promote the production technology innovation towards to green sustainable chemistry, a pipe flow reactor equipment was introduced as a new technology in late 2013. It is a gas-liquid reactor which maximizes the performance of homogeneous catalysis, which is our core technology. Compared to existing batch reaction (autoclave), potential risk is remarkably reduced by residing hydrogen quantity becomes under 1/15. Also, because this equipment doesn’t require a big agitator, agitation efficiency by small pump is increased and as a big agitator is not required and a small liquid delivery pump is used, the electricity usage is reduced to 1/10.
In introduction of a flow reactor, we performed risk assessment (HAZOP) multiple times in participation of Production department, Technical development department, Quality assurance department, and Facility department in order to improve safety. Also, as our efforts to the innovation in production, we are aiming to the establishment of efficient continuous flow production method. Making introduction of a flow reactor as the beginning, we will promote process innovation towards to intermittent–continuous stirred tank reactor (I-CSTR), continuous crystallization, continuous filtration, and full-automatic continuous production.
Reduction of Environmental Load
By optimizing our unique catalyst technology, we have shortened the production process of organic electronic materials (OPCs), and have realized remarkable saving of energy and resources. Efforts were also made to reduce energy usage and industrial waste emission. It had resulted 10% reduction of electricity usage and 16% reduction of the groundwater and industrial water usage in 2013 compared with previous year. Also, as an effort made in power peak cut, we implemented a private generator. We will keep actively engaging in the reduction of environmental load.
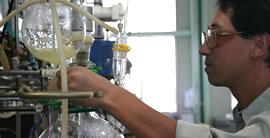
Social Contribution Activity
Contribution to local environmental activity
We actively participate in social contribution activities closely related to local communities, such as clean-up campaign in the surrounding area of factory, seashore cleaning project, a tree planting in the forest reserve planted along the coast, and cleanups of illegally dumped waste in the area.
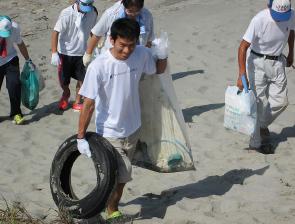
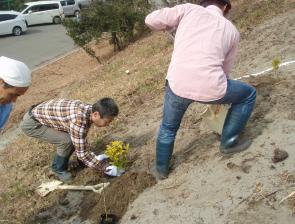
A fuel oil A-boiler had been used at Kakegawa factory, but as the supply of gas pipelines commenced in January 2015, we introduced a natural gas boiler facility. Less CO2 and NOx (nitrogen oxides) are released compared with a heavy oil boiler, and the generation of SOx(sulfur oxides)and the dust to cause air pollution became almost zero. We will keep engaging in efforts to reduce energy consumption by efficient operation.
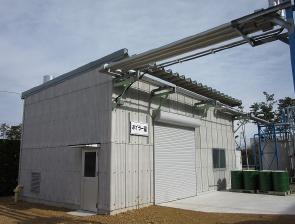
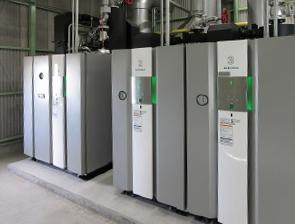