Basic Policy
Takasago is a committed valuable partner of our customers, meeting all their product quality, regulatory and safety requirements. The mission of the Corporate Quality Assurance Headquarters (QAHQ) is to ensure that Takasago supplies safe, wholesome and reliable fragrances, flavors, aroma ingredients and fine chemicals that comply with the safety and regulatory requirements of local governments, customers and trade associations. To achieve this mission, we promise to pursue “no complaints, no non-conformities” and “no defects, no errors.“
Quality Assurance Organization
Takasago QAHQ strives to ensure that Takasago consistently delivers high-quality products and ensures that our customers’ needs are met. QAHQ is an independent organization within Takasago composed of quality assurance departments around the world that operate under the One Takasago Quality Assurance Concept. QAHQ includes four centers: the Global Flavor QC Center (FLQC), the Global Fragrance QC Center (GFQC), the Global Flavor Regulatory Center (GFRC) and the Global Fragrance Safety and Regulatory Affairs (GFSARA) Center which operate globally and closely with local affiliates. These four centers are responsible for the development and implementation of global policies and guidelines under a globally standardized operation process. Both Flavor and Fragrance QC Centers strive to standardize, maintain and enhance the QC testing skills of the local QC team by conducting sensory evaluation, physicochemical testing and microbiological testing proficiency tests. Both QC Centers supports the quality standardization of raw materials which are used globally to provide the same quality products in collaboration with the procurement department. We believe these activities will contribute to not only the quality aspect of all products that we manufacture, but also to ensure that a continuous supply of products can be provided to our customers in the event when the business continuity plan (BCP) must be implemented. Aside from the globally recognized regulations, both GFRC and GFSARA communicate with specific national trade associations and working groups to stay up to date on the latest regulatory information and changes globally. This information is shared and updated with the team members of all affiliates. The latest information alerts enable all team members at all affiliates to use the latest regulatory information for product labeling, customer support and informative purposes. This has allowed the local affiliates to consistently provide the support that our customers need.
The global regulatory teams have been also very effective in developing new functionality to prepare for new regulatory requirements. This includes the development of new auto-generated forms to address new regulatory requirements and supports new customer requirements. In addition, the global regulatory teams have implemented global tracking systems for CAPA plans to better recognize commonly arising issues. This allows the global teams to be more effective in developing proactive policies and procedures to reduce non-conformity across the globe. Thus, we are able to provide the highest quality products to meet or exceed all of our customers’ expectations worldwide.
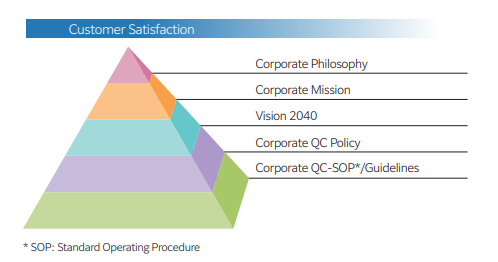
QC Policy, SOP and Guideline
Takasago’s Corporate QC Policy was developed based on our Corporate Philosophy, Corporate Mission and Charter of Corporate Behavior. The policies promotes a globally consistent quality mindset and systems that not only meet our customer’s expectations, but also ensure appropriate and timely improvement to our day-todayactivities in line with the Corporate QC Policy, global QC Standard Operating Procedures (SOPs) and guidelines were established to standardize detailed QC procedures across all business units and affiliates. These guidelines are also incorporated in the local quality management procedures and practices to ensure the global alignment of QC management.
Compliance with Laws and Regulations Related to Chemical Substances
It is Takasago’s global policy to comply with the latest laws and regulations. Takasago fully supports the objective of the chemical legislation around the world to improve the safe and sustainable use of chemicals and improve the quality of life of all citizens of the world and the environment. To conduct our business globally, The Takasago Group complies with laws, regulations, and relevant standards on product quality and safety, the environment and chemical substances as well as on accounting, taxes, labor and transactions in each country and region. This includes compliance with laws and regulation related to chemical substances, and The Takasago Group considers this to be a top priority. We continuously monitor and complete regulatory activities to ensure that we meet local regulatory requirements around the globe. This applies to the four business pillars of The Takasago Group, the Fragrance, Flavor, Aroma Ingredients and Fine Chemicals divisions. To comply with the regulations of various regulatory bodies, The Takasago Group works as a global team to ensure that registration activities around the globe are conducted efficiently, minimizing redundancy in testing and expediting registration. As we look towards 2023 and beyond, there are number of new chemical laws that are currently being written and may require The Takasago Group to conduct additional registration activities. These laws include UK REACH, potential updates to the EU REACH requirements, Turkey-REACH and other chemical legislation. As new chemical legislation are enacted, The Takasago Group will be ready to work proactively to meet new compliance requirements. The GFSARA continuously monitors ever- changing global regulations, customer requirements, standards and guidelines by communicating with trade organizations such as the IFRA1 , IOFI2 , FEMA3 , EFFA4 . ACI5 PCPC6 and many other trade associations. Information is shared promptly with each affiliate around the world, guaranteeing that Takasago can provide safe and reliable products all over the world in a consistent manner.
1 IFRA: International Fragrance Association
2 IOFI: International Organization of the Flavor Industry
3 FEMA: Flavor and Extract Manufacturers Association
4 EFFA: European Flavour Association
5 ACI: American Cleaning Institute
6 PCPC: Personal Care Products Council