Takasago International Corporation Hiratsuka Factory caused two serious accidents in 2013. We sincerely apologize to neighborhood, the authorities concerned, our customers, and the many others who were seriously inconvenienced by these accidents.
In response to the accident, existing facility was restored and started its operation in October 2013 as a new factory.
Learning a lesson from two accidents, Hiratsuka factory will further reinforce safety measures in order to regain the trust of stakeholders, including local communities, neighboring companies, and business partners.
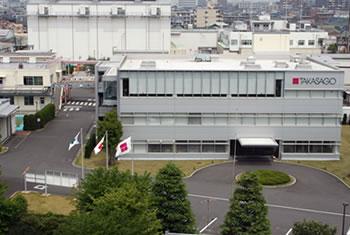
Implementing Measures to Prevent Recurrence
Hiratsuka factory is taking the following safety measures at all production facilities;
- Introduction of conductive dollies.
- Securing of conductivity of floor by switching to metallic floor, coating with conductive paint and application of conductive tape.
- Installation of local exhaust arrangement
- Review of the operation procedure
- Education of static electricity and dangerous substances
- Revision of risk assessment
- Implementation of fire extinguishing training
- Maintenance of leakage countermeasures
Other than the above, observations from the internal safety inspection will be successively improved.
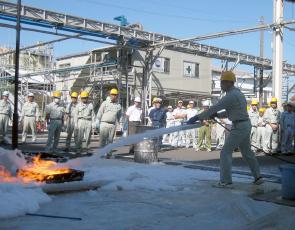
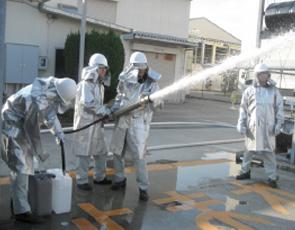
Aiming to be a Neighbor-friendly Factory
Efforts have been made to achieve “Zero odor complaint from neighboring residents” by such as conducting odor patrol on and around the factory. Also, by installation of local exhaust arrangements, we will improve working environment and reinforce prevention of diffusion of odor.
5S / Kaizen activities
At the Hiratsuka Factory, we have set up an "Executive Inspection Day," a surprise inspection by the Executive at different points around the factory each month to check the status of the 5S/Kaizen* activities in daily operations. The reason for this inspection is to encourage the natural implementation of the 5S/Kaizen activities to daily business operations. Also, we are engaged in the Kaizen suggestion system which the employees themselves create and propose plans to address points requiring improvement in 5S and business activities. We will continue to promote the 5S/Kaizen activities across the organization.
The 5S's are: seiri (sorting), seiton (setting in order), seiso (systematic cleanup), seiketsu (sanitizing), and shitsuke (sustainable discipline).
Environmental Management System
Hiratsuka Factory and the Takasago group acquired global integrated ISO14001 certification in 2011, and we are also engaged in EMS, QMS, and food safety. All employees participated external educational training in 2014. The roads on the premises which may become risk factor and environmental load were repaired to establish safe working environment. We will keep promoting green management based on EMS hereafter.
Energy Saving / Environmental Loading Reduction
In 2013, we reduced electric power consumption by switching equipments, such as a root blower of wastewater treatment facility, to an energy saving type. In 2014, we went a step further and reduced 2,000 kWh/month of electricity power consumption by reducing the load of a root blower by renewal of aeration pipe of aeration tank in the wastewater treatment facility. We also have made effort to reduce CO2 emissions by converting forklifts from diesel to electric power.
20m3 of discharge amount of a groundwater per month was reduced by circulating final effluent of a wastewater treatment facility.
We will make continuing effort to reduce an environmental load by the reduction of CO2 emissions, water consumption, and waste generation.